Featured Resources
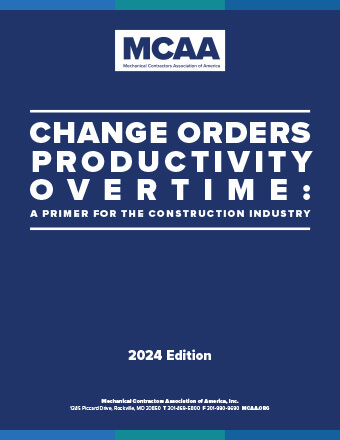
Change Orders, Productivity, Overtime—A Primer for the Construction Industry
This planning tool helps you determine the costs associated with unplanned events, circumstances and factors that may impact the outcome, productivity and schedule of construction projects. New for 2024: a chapter exploring the factors that contribute to BIM cost and time overruns.
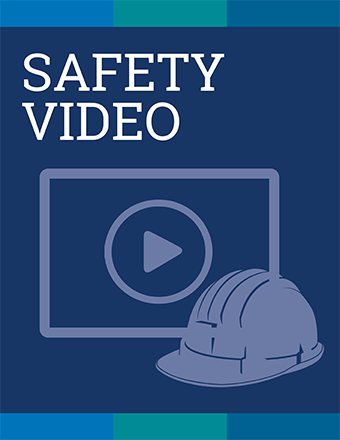
Mental Health Awareness & Suicide Prevention Video
Our newest safety and health video highlights the success story of an industry veteran, with appearances from MCAA’s president Robert Beck, the UA’s Jen Massey, industry expert Dr. Sally Spencer Thomas, and MCAA member Ricky Reams.
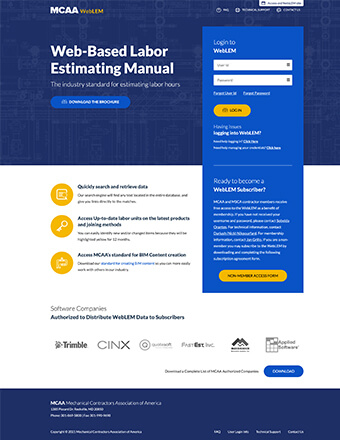
WebLEM is the industry’s most reliable authority for comprehensive labor units for typical project tasks. Quickly search for and retrieve information. WebLEM is reviewed and updated to reflect the latest products and joining methods. You will need your MCAA.org username and password to log in to WebLEM. For WebLEM access questions, please refer to the WebLEM Access FAQs page.
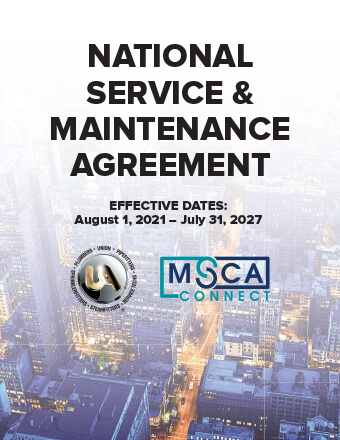
National Service and Maintenance Agreement
The National Service and Maintenance Agreement is an agreement negotiated and administered by the United Association of Journeymen and Apprentices of the Plumbing and Pipefitting Industry (UA) and the Mechanical Service Contractors of America (MSCA) and is a signed contract between the UA and individual mechanical service contracting firms who apply and qualify. The Agreement is a nationally recognized tool that helps contractors provide quality, consistent service to their customers throughout the country and helps reclaim lost market share.
MCAA’s Virtual Trade Show connects our contractor members with the members of MCAA’s Manufacturer/Supplier Council.
Switching from manual hoists to MILWAUKEE TOOL’s M18™ Compact 1-Ton Chain Hoist with ONE-KEY™, Hooper Corporation minimized the physical demands on its workers while making installation much easier and decreasing downtime. Using a cordless chain hoist takes less time to set up and also allows Hooper’s team to get into more tight spaces, increasing efficiency overall. MILWAUKEE TOOL is a benefactor of MCAA25.
Registration is now open for MCAA’s May Field Leaders Conference, being held Monday, May 12 – Wednesday, May 14 at the Hilton Washington DC National Mall The Wharf. In two and a half days, your field leaders will hear from inspiring industry speakers and participate in powerful collaboration, leaving them inspired and re-energized. Don’t miss this opportunity to register your field leaders today.
As a business owner in the mechanical contracting industry, you already juggle enough—projects, workforce management, regulations, and keeping up with an ever-changing market. But what happens in Washington, D.C. directly impacts your bottom line. The CEA National Issues Conference is your chance to influence the policies affecting your business, rather than just reacting to them after they’re set. This is your chance to shape the future of the mechanical contracting industry. Don’t just watch the change—be part of it. Register today!
As part of its ongoing commitment to protecting your livelihood and setting the stage for a bright future, MCAA has secured the services of Longbow Public Policy Group to advise our MCAA Government Affairs Committee (GAC). GAC Chair, Jim Gaffney will be passing along information relative to our industry on a regular basis.
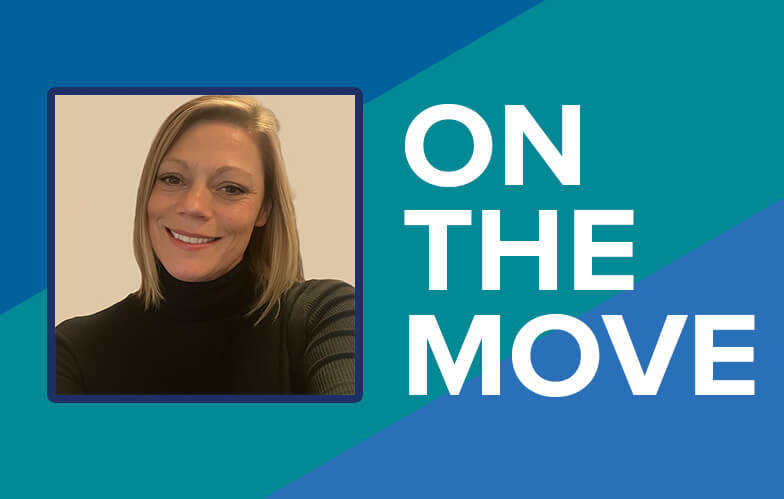
Heather Roberts is the MCA of New Jersey, Inc.’s new Office Manager. Her many years of experience working with unions and union members as a Medical Claims Supervisor for a Union Benefit Funds Administrator prepared her for the role. As she puts it, “I feel at home again at MCANJ.”
Brady is a Construction Management major at the University of Nebraska at Omaha with an anticipated graduation of May 2026. He has been an active member of his student chapter since 2022 and has served as both Treasurer and Vice President. This summer, he is interning with MCAA Member, Prairie Mechanical Corporation.
Some serious health hazards aren’t obvious, like those affecting hearing, breathing, or the ability to move, and the effects of these hazards can take time to develop. MCAA’s Health Hazards in Mechanical Construction Safety Training Video provides tips for protecting your health so these hazards don’t lead to lifelong issues. It’s just one of MCAA’s educational resources that are free to MCAA members as a benefit of membership.
Welcome to Inside MCAA, The Blueprint to Mechanical Contracting, the podcast dedicated to unveiling the strategies and resources that power success within the Mechanical Contractors Association of America. Hosted by renowned Customer Experience Coach and NEI Instructor Frank Favaro, each episode dives deep into the wealth of educational tools, networking opportunities, and advocacy efforts that define MCAA.
When choosing which projects to bid on, mechanical construction contractors must evaluate several factors to ensure the project is a good fit for the company and has a high probability of success. MCAA’s new Management Methods Bulletin, How Do I Pick a Project?, explores the factors that go into making an informed decision that will increase your company’s chances of successfully winning the bid and completing the project. It’s just one of MCAA’s educational resources that are free to MCAA members as a benefit of membership.
Don’t miss out on the upcoming PCA Plumbing Service Conference! May 19-21, 2025, in St. Louis, this event is your best opportunity to learn, share, and grow in your understanding of operational plumbing service. With industry leaders, in depth tours, and invaluable networking, this is a conference you don’t want to miss. Sign up now!
The ripple effect of change begins with one small action – and in the mechanical industry, women are making waves. The WiMI Conference offers an unparalleled opportunity to connect with like-minded professionals, gain valuable knowledge, and be inspired by the journeys of those who have dared to lead. Whether you’re new to the industry or a seasoned executive, the WiMI Conference is a platform for you to find your voice and expand your influence within the industry. Join us at the WiMI Conference – empower yourself, connect with others, and leave ready to make your mark on the industry. Register now!
MCAA’s web-based labor estimating manual is an invaluable tool for your business. Free as a benefit of your membership.
WebLEM
Scholarships are just one way the John R. Gentille Foundation is investing in your industry’s future. Have you invested in it?
JRGF
You can make an impact on the future of your industry and your business by contributing to the MCAA Political Action Committee.
MCAA PAC
Looking for an intern? You can head to our improved student chapter website and check out the great resumes there!
MCAAGreatFutures
The year-round involvement of our manufacturer/supplier members is part of what makes MCAA special. Learn more about the Council and the value it brings to MCAA.