Featured Resources
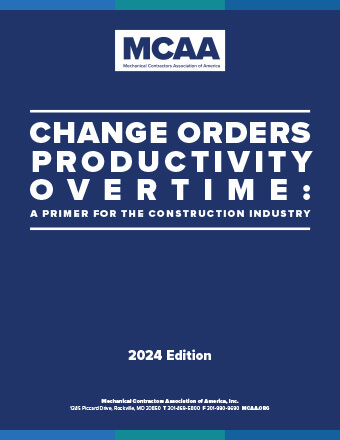
Change Orders, Productivity, Overtime—A Primer for the Construction Industry
This planning tool helps you determine the costs associated with unplanned events, circumstances and factors that may impact the outcome, productivity and schedule of construction projects. New for 2024: a chapter exploring the factors that contribute to BIM cost and time overruns.
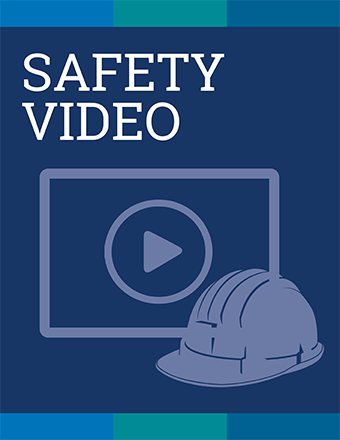
Mental Health Awareness & Suicide Prevention Video
Our newest safety and health video highlights the success story of an industry veteran, with appearances from MCAA’s president Robert Beck, the UA’s Jen Massey, industry expert Dr. Sally Spencer Thomas, and MCAA member Ricky Reams.
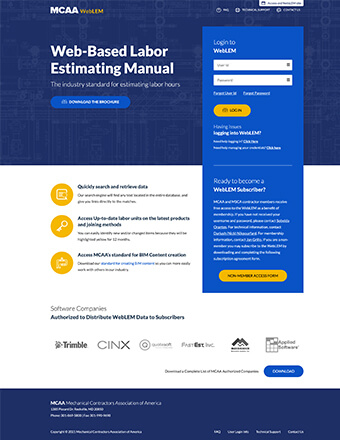
WebLEM is the industry’s most reliable authority for comprehensive labor units for typical project tasks. Quickly search for and retrieve information. WebLEM is reviewed and updated to reflect the latest products and joining methods. You will need your MCAA.org username and password to log in to WebLEM. For WebLEM access questions, please refer to the WebLEM Access FAQs page.
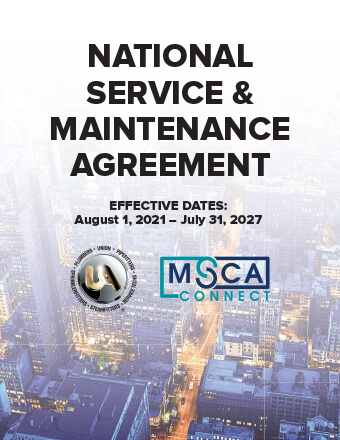
National Service and Maintenance Agreement
The National Service and Maintenance Agreement is an agreement negotiated and administered by the United Association of Journeymen and Apprentices of the Plumbing and Pipefitting Industry (UA) and the Mechanical Service Contractors of America (MSCA) and is a signed contract between the UA and individual mechanical service contracting firms who apply and qualify. The Agreement is a nationally recognized tool that helps contractors provide quality, consistent service to their customers throughout the country and helps reclaim lost market share.
Field leaders are one of a contractor’s most valuable assets. Energize your field leaders and build their skills with MCAA’s Field Leaders Conference. Watch the video to hear what other contractors have said about the program, then sign up your field personnel. Register them before October 21 and save with early bird rates!
MCAA’s Virtual Trade Show connects our contractor members with the members of MCAA’s Manufacturer/Supplier Council.
If you want to fast-track your new and aspiring field leaders, MCAA has just the program! Once a week for 8 weeks, FFL students spend 90 minutes online with an experienced field leader, who will walk them through best practices and practical strategies of running work and running a crew. From Planning to Leadership, from Documentation to Safety: our instructors break down the ‘why’ and the ‘how’ of things that every foreman must understand to be successful.
The Sunday Night Opening Party at the MCAA Annual Convention is always an attendee favorite. It’s the first opportunity to see old friends, to grab a bite and drink with a colleague and to unwind and get ready for a fantastic week of education, entertainment and excitement with some great country music and dancing to round out the night. Don’t forget to register for MCAA25 to be a part of this memorable night.
MCAA is deeply heartbroken by the tragic crash of American Airlines Flight 5342 on January 29. MCAA stands ready to support our members in need during this difficult time. We stand with the families of the four UA Local 602 members and one UA Local 5 member who were passengers on the flight. They and all the passengers will remain forever in our hearts—may they rest in peace.
Companies that let employees use company vehicles may face liability should an accident occur. MCAA’s Avoiding Potential Liability from Employees’ Use of Company Vehicles describes the most common types of liabilities and offers tips to help reduce them. It’s just one of MCAA’s educational resources that are free to MCAA members as a benefit of membership.
The Regular Rate Deadline of January 31, 2025, is here! Register for MCAA25 today to lock in the Convention’s most favorable registration rates.
We’re thrilled to announce a new collaboration between MSCA and the EMCOR Training Center in Phoenix, AZ. This state-of-the-art training center provides technical training for your service techs, from fundamentals to specifics. With a facility that offers both classroom and hands-on learning, you can keep your techs up to date on the best practices and most recent equipment for the industry.
The Construction Labor Research Council (CLRC), a longstanding MCAA partner, reports an average increase of 4.7 percent in the first year of new settlements reached in 2023 for union craft workers in the construction industry. The findings appear in the CLRC 2023 Year End Settlements Report. The report covers the first year of newly bargained settlements to assist readers in understanding current trends. It also covers all years of negotiated settlements to assist in projecting future labor costs.
The Manufacturer/Supplier Training area of MCAA’s website connects our contractor members with training opportunities available from the members of MCAA’s Manufacturer/Supplier Council.
On February 6, 2025, at 2:00 p.m. EST, Daniel Bunn, President & CEO of the Tax Foundation, will provide an in-depth analysis of expected federal policy changes during the second Trump administration. The session will be moderated by Jim Gaffney and Chuck Daniel. Don’t miss this opportunity to gain valuable insights from a leading expert in the field.
The NCPWB Technical Conference is just around the corner! Don’t miss this exciting opportunity to learn, share, and connect. This year’s conference is packed with valuable content and unmatched opportunities to network with friends, colleagues, and new acquaintances. We’re also introducing for the first time, an exhibitor showcase on Monday afternoon where you can see the latest and greatest welding technologies. Don’t miss it – register today!
MCAA’s web-based labor estimating manual is an invaluable tool for your business. Free as a benefit of your membership.
WebLEM
Scholarships are just one way the John R. Gentille Foundation is investing in your industry’s future. Have you invested in it?
JRGF
You can make an impact on the future of your industry and your business by contributing to the MCAA Political Action Committee.
MCAA PAC
Looking for an intern? You can head to our improved student chapter website and check out the great resumes there!
MCAAGreatFutures
The year-round involvement of our manufacturer/supplier members is part of what makes MCAA special. Learn more about the Council and the value it brings to MCAA.