Find A Resource
Use the form below to find the specific solution to your challenge and advance your business.
Featured Resources
P.J. Dionne Company found that using Sloan’s AER-DEC® Integrated Sinks helped make a complex installation at Logan Airport a more collaborative effort. (SLOAN is a benefactor of MCAA25.) Sloan’s AER-DEC Integrated Sinks contribute to the airport’s sustainability goals while offering high standards of hygiene and efficiency.
Welcome to Inside MCAA, The Blueprint to Mechanical Contracting, the podcast dedicated to unveiling the strategies and resources that power success within the Mechanical Contractors Association of America. Hosted by renowned Customer Experience Coach and NEI Instructor Frank Favaro, each episode dives deep into the wealth of educational tools, networking opportunities, and advocacy efforts that define MCAA.
MCAA member contractors and local affiliates are encouraged to participate in an upcoming UA organizing blitz. This is a great opportunity to share the benefits of working for a union contractor and enhance the labor/management relationship. Read on to learn more, then register for a blitz near you.
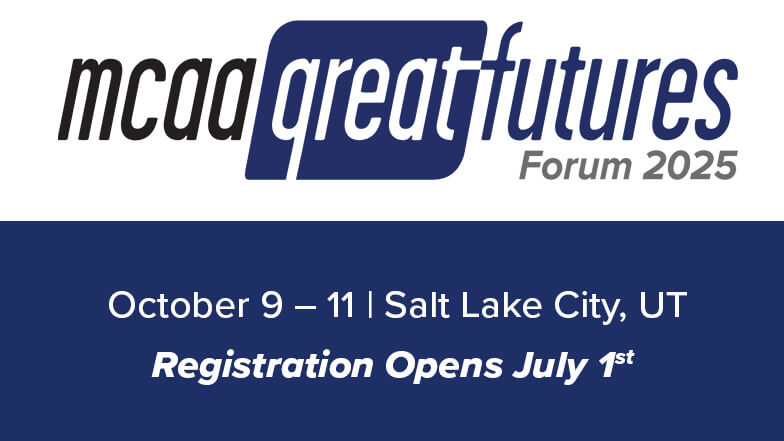
Although summer ’25 isn’t quite here yet, it’s already time to start the process for securing your summer ’26 interns! Save the date for the 2025 MCAA GreatFutures Forum (October 9-11, 2025) in Salt Lake City, Utah. Conference registration, including the Job Fair, is complimentary for MCAA Members, MCAA Student Chapter Members, Faculty Advisors, Affiliated Association Executives and Forum Sponsors. Registration will open on July 1st.
The National Safety Stand-Down to Prevent Falls in Construction and Construction Safety Week are coming up May 5-9. The Safety Alliance of MCAA, TAUC, SMACNA and NECA has created five new videos for employers to share during safety meetings and stand-down events.
New workers are often the most vulnerable to accidents and injuries. MCAA’s New Worker Safety & Health Resources assist contractors in providing training on how to identify common hazards in the mechanical industry, and how to protect themselves from those hazards. Topics covered include stop work authority, pre-task planning, PPE, working at heights, fall protection, fall prevention, power tool safety, hazard communication, housekeeping, and emergency procedures. These are just a few of MCAA’s educational resources that are free to MCAA members as a benefit of membership.
Hurckman Mechanical Industries (HMI), an MCAA member, was awarded the prestigious Wisconsin Workplace Safety Award on April 14, 2025, for medium-sized construction companies. The award was given by the Wisconsin Safety Council (WSC), the state’s leading provider of safety training and products. This honor is a significant achievement—only about 200 companies have received it in the past 31 years.
The Manufacturer/Supplier Training area of MCAA’s website connects our contractor members with training opportunities available from the members of MCAA’s Manufacturer/Supplier Council.
MCAA’s Virtual Trade Show connects our contractor members with the members of MCAA’s Manufacturer/Supplier Council.
The PCA Plumbing Service Conference is right around the corner – happening May 19–21 in St. Louis, MO – and there are only a few spots left! Don’t miss out on your best opportunity to learn, share, and grow in your understanding of operational plumbing service. With industry leaders, in depth tours, and invaluable networking, this is a conference you don’t want to miss. Sign up now!
Field leaders looking to enhance their leadership skills and industry knowledge will benefit from MCAA’s May Field Leaders Conference, being held Monday, May 12 – Wednesday, May 14 at the Hilton Washington DC National Mall The Wharf. The event is nearing full capacity. Don’t miss this opportunity to register your field leaders today!
Aidan Wolownik, is studying construction management at Pittsburg State University and is anticipated to graduate this May. Aidan has been a member of the student chapter since 2022 and has held the roles of Fundraising Chair and President. Upon graduation, Aidan will join MCAA Member, Lippert Mechanical Service Corporation as an Assistant Project Manager.
MCAA’s web-based labor estimating manual is an invaluable tool for your business. Free as a benefit of your membership.
WebLEM
Scholarships are just one way the John R. Gentille Foundation is investing in your industry’s future. Have you invested in it?
JRGF
You can make an impact on the future of your industry and your business by contributing to the MCAA Political Action Committee.
MCAA PAC
Looking for an intern? You can head to our improved student chapter website and check out the great resumes there!
MCAAGreatFutures
The year-round involvement of our manufacturer/supplier members is part of what makes MCAA special. Learn more about the Council and the value it brings to MCAA.