Silicon Valley Mechanical Improves Productivity, Efficiency With PypeServer Enterprise Software
Silicon Valley Mechanical, a full-service mechanical contractor in San Jose, CA, rapidly improved productivity and increased efficiency by putting PypeServer software into place. Here, Jamie Garza, detail manager, and Dean Garza, piping shop general foreman at Silicon Valley Mechanical, describe how they achieved those gains.
What led to your decision to try PypeServer’s workflow software?
We’ve been running PypeServer’s Enterprise software for our Vernon pipe profiler since early 2021 and have been happy with it. Between its O-let handling features, part nesting, and labeling, Enterprise is giving us two to four times the productivity and higher cut quality from our Vernon. At the same time, we’d tried several different workflow software packages from other vendors to get data from our VDC [virtual design and construction] group to the shop, but nothing really worked to our satisfaction. We recently had a connectivity issue between another piece of software and the Vernon—it would just stall out for days with no help from the vendor. That’s what led us to try PypeServer’s Connect and Cloud workflow software, which is included for free with our Enterprise subscription for the Vernon.
Learn more about the software and request a demo here: https://bit.ly/3w2M7Xu
What does your typical workflow look like now, from design through production?
The Detailing team works with engineered drawings in AutoCAD Fabrication CADmep to set them up for prefabrication. Once a model is signed off and ready for build, we spool in Fabrication, select the parts we want to cut using the PypeServer Connect plug-in for AutoCAD, and send the cut lists to the Vernon using the PypeServer Cloud service to transmit the data and monitor progress.
You’re one of the first users of PypeServer’s full suite of workflow products, including the Connect add-ons for Revit and AutoCAD, the Cloud service, and PypeServer Enterprise for your Vernon MPM pipe profiler. Can you describe the implementation process?
Getting everything set up and working was much easier and faster than we expected. We worked with the PypeServer Support team to understand how information gets pushed through the system and how to configure PypeServer Connect and Cloud to send data to our Vernon. Installing the Connect add-on for AutoCAD is a breeze, and it’s simple to add users to our Cloud account. It literally takes only minutes to train someone new on the PypeServer workflow, and they’re pushing data to the shop in under an hour. PypeServer’s support team also helped us set things up on the shop side with Enterprise for the Vernon. The software lets us automatically customize O-let hole sizes, insert root gaps, and make other fabrication-specific design tweaks, as well as printing labels.
Having the PypeServer team available for support has been huge. When we’re up and rolling, we don’t have days to stop if something goes wrong. We need to be back up and running within hours, and PypeServer has delivered.
How has your workflow changed with PypeServer, and what savings in time, labor, and materials have you seen?
Our VDC group used to spend a lot of time converting feet and inches to decimals on spool sheets for the shop. When you look at the number of spools we build, the time spent on that adds up fast. Now the Vernon pipe profiler gets the information it needs directly from the Connect AutoCAD plug-in, so the process has been streamlined from a page-by-page spool sheet review that could take hours to a quick five minutes to send the data to the cloud, bring it into Enterprise, and double check that everything that needs to be fabricated was sent down to the shop from VDC.
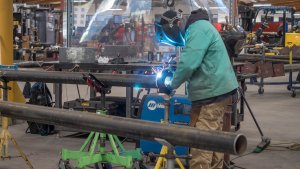
The nesting feature of Enterprise is also a huge time and material saver. Now we can send all the parts to the machine at the same time, and it will cut them in one operation with minimal waste. This allows the operator to accomplish other tasks, like prepping the ends of the pipe for the welder, organizing the pieces coming off the Vernon, and then loading new material to be cut.
Our workflow is now migrating toward pushing everything to PypeServer Cloud. We used to rely a lot on cut files that we’d put in specific folders on our computer network. Sometimes files would get put in the wrong place and it was possible to accidentally cut things twice. With the Cloud, there are no lost files and the system keeps track of what’s been cut.
PypeServer Enterprise for the Vernon easily paid for itself before we started using Connect and Cloud, but now the efficiencies are extending up to our VDC group, and we don’t have to pay anything extra for those workflow tools.
Do you have any further improvements planned for your fabrication process?
We really like how PypeServer Enterprise has increased the value of our Vernon pipe profiler, and we’re looking at using PypeServer Lyte with our TigerSaw. Many of our projects include fabricating specialty racking systems out of copper. We cut all this on our TigerSaw, and a lot of the pieces can be prefabricated. We’ve already been testing the new workflow, pulling cut lists from AutoCAD and sending them to the TigerStop using Connect and Cloud in exactly the same way we do for the Vernon.
Are there any other benefits that you didn’t expect from the PypeServer software?
We really like how PypeServer Enterprise gives us deep control over how the Vernon works. For example, the Vernon has a big rotating head that gives it a lot of beveling flexibility, but for small holes, it can slow things down and cause overburn. Enterprise lets us turn off head rotation for small holes, which really speeds it up and improves cut quality dramatically. We’re now able to cut holes as small as 3/16”. With the regular Vernon software, we couldn’t do that.
Do you have any advice for other organizations looking to improve their fab shop productivity?
Be patient and have a clear road map for where you want to go. We recommend tackling one piece of equipment at a time and making sure you have a dedicated test team who can stay on top of the process to refine the workflow. Ask your peers what they are doing, where they are finding opportunities for success, and also where they’ve come up short.
In the end, we really like the way PypeServer has removed the middleman between VDC and the shop. We get great visibility on cut lists as they move from the design software to the pipe profiler—giving us more control and better efficiency.
For more information, visit pypeserver.com.