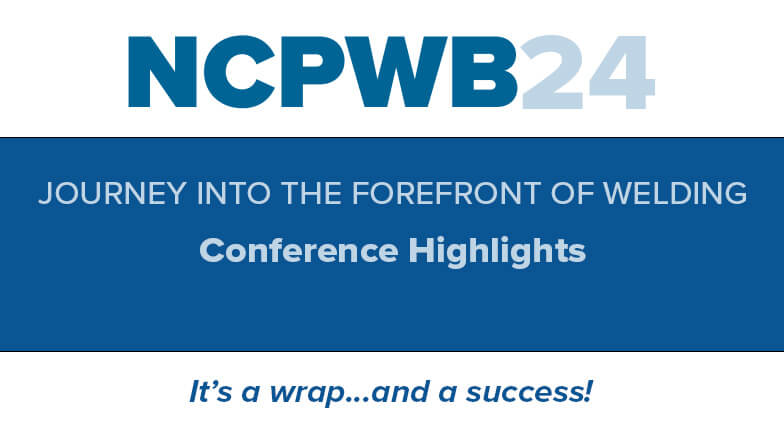
The NCPWB Technical Conference/Committee Meeting showcased advancements and innovations in the field of welding technology. Attendees learned about the latest developments in pipe welding techniques and the application of orbital welding technology in medical gas systems. A case study on adaptive welding demonstrated its practical implementation and recent advancements, highlighting its potential in various industries. The importance of education and automation for future business success was emphasized, underscoring the need for continuous learning and technological integration. High-purity tube welding was discussed, addressing the unique challenges and advancements in this specialized area. Additionally, the conference covered the intersection of welding and additive manufacturing, exploring both the progress and remaining hurdles in this evolving field.

The Miller Electric Mfg. Co. presentation by Craig Spindler and Steve Hidden illuminated the forefront of pipe welding advancements, showcasing a blend of educational resources and cutting-edge technologies. These advancements signify a leap forward in pipe welding, promising enhanced efficiency, quality, and adaptability, from the precision of RMD technology for root passes on both carbon and stainless steel to the finesse of Pulse technology for fill and cap passes.
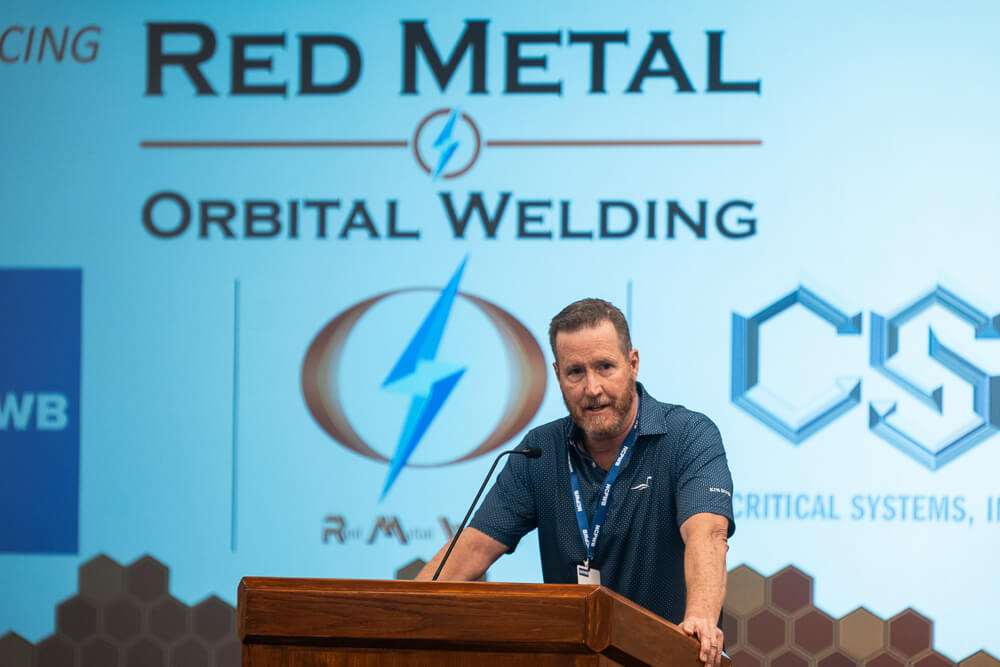
CSI emerged as a pioneer in the realm of orbital welding technology for medical gas piping with a focus on research and development in computer-operated welding equipment. Theodore J. Jones and Lynne Cooper with CSI unveiled a game-changing universal power supply alongside copper orbital welding machines designed to elevate quality standards in various applications. Years of dedicated efforts have led to this milestone, but not without its fair share of challenges. CSI’s presentation shed light on the hurdles faced, including navigating complex metallurgical properties, temperature considerations, and stringent code requirements. They are overcoming these obstacles by developing solutions that address the intricacies of materials and code compliance, ensuring reliability and safety in the commercial market.
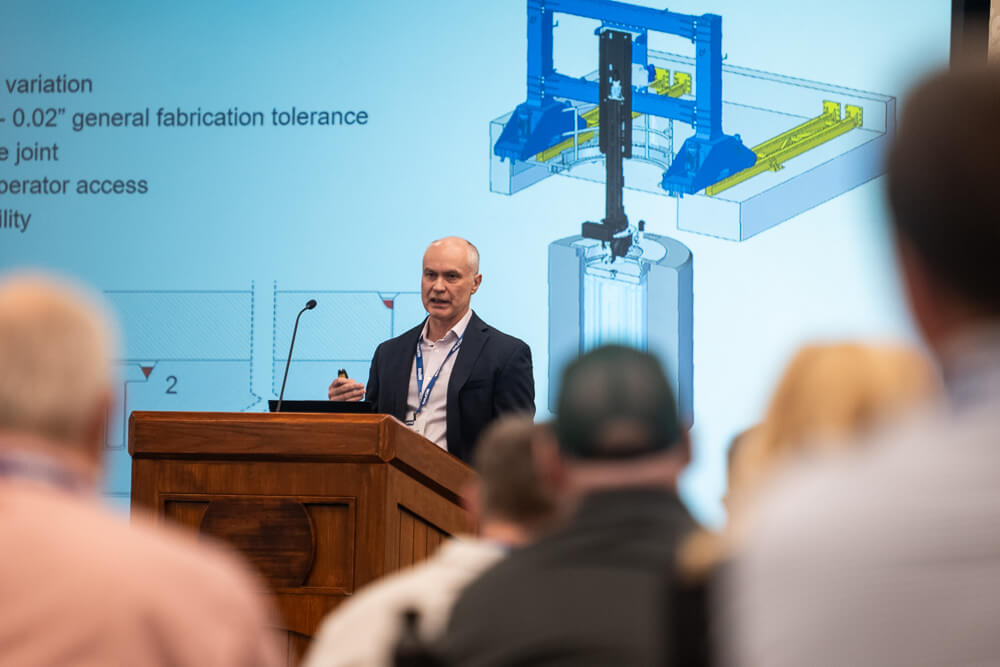
Janusz Bialach with Liburdi Dimetrics presented a groundbreaking case study on adaptive welding. The presentation described a first-of-a-kind welding system that will be used for encapsulation of spent nuclear fuel at the DOE Hanford Site. Unlike traditional methods, which rely heavily on operator input, this innovative approach minimizes or eliminates the need for human intervention during closure welds. This shift in paradigm necessitated the development and integration of autonomous technology, including active path compensation and adaptive welding parameters. A highlight of the presentation was the use of Artificial Intelligence to characterize joint geometry, providing vital data for the adaptive algorithms. This cutting-edge technology opens doors to a myriad of applications beyond nuclear encapsulation, including pipe welding.
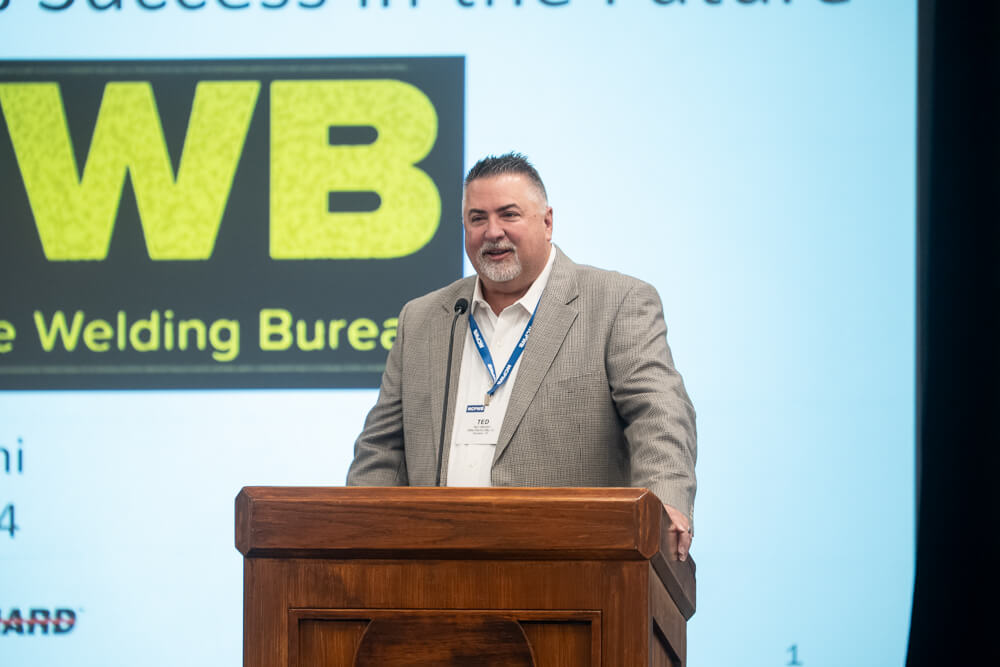
Ted Valentini with Miller Electric Mfg. Co. addressed the pressing issue of the welder shortage, now exceeding 400,000 and rising. The shortage demands urgent attention by industry leaders. He emphasized the critical need to rethink strategies and take decisive action to address this challenge before it escalates further. To combat the deficit, a multifaceted approach is essential. Education stands at the forefront, with a call to actively engage and train more individuals in welding. However, traditional methods alone cannot meet the growing demand. Innovative technologies such as Augmented Reality and Virtual Reality Systems are revolutionizing the educational landscape, catering to diverse learning styles and preferences. Companies must adapt or face the risk of obsolescence in the coming decade. Embracing education and automation isn’t just a choice; it’s a necessity for ensuring business longevity and success in the evolving landscape of the welding industry.

The term “High-Purity Welding” may seem misleading at first glance, suggesting that the welds themselves possess exceptional purity. However, Lynn Sturgill with Sturgill Welding and Code Consulting believes that the essence lies in constructing piping systems that uphold stringent standards to prevent contamination of the fluids they handle, particularly in pharmaceutical manufacturing. Fabricators must grasp the examination requirements outlined in ASME B31.3, adhere to the weld acceptance criteria of the ASME BPE Standard, and ensure welding operators meet additional qualification standards. In essence, high-purity welding isn’t about the purity of the welds per se, but rather about adhering to rigorous standards to safeguard the integrity and purity of pharmaceutical products.
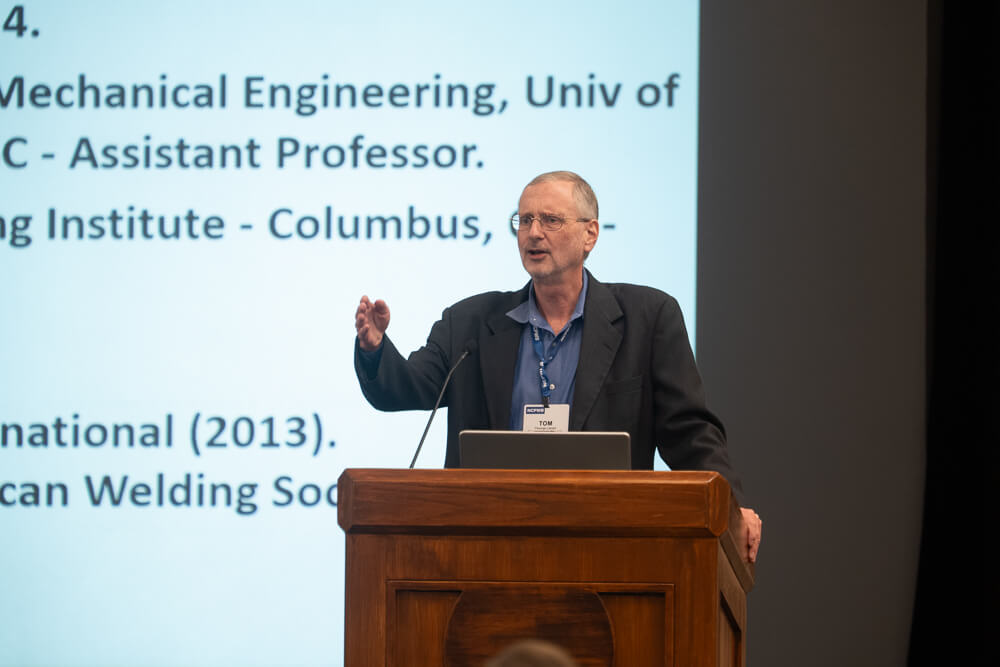
Attendees were treated to a comprehensive presentation by Dr. Thomas J. Lienert of Lienert Consulting that delved into the latest developments at the intersection of welding and additive manufacturing (AM). The session kicked off with an overview of cutting-edge welding processes, including pulsed GMAW, STT/CMT GMAW, Hyperfill, TOP TIG, and manual LBW, accompanied by engaging videos showcasing these techniques in action. Automation took center stage as well, with a focus on the utilization of cobots for welding and inspection, promising enhanced productivity and efficiency. The presentation didn’t stop there, as attendees were treated to insights into the latest advancements in laser welding, with captivating videos highlighting the capabilities of this technology.
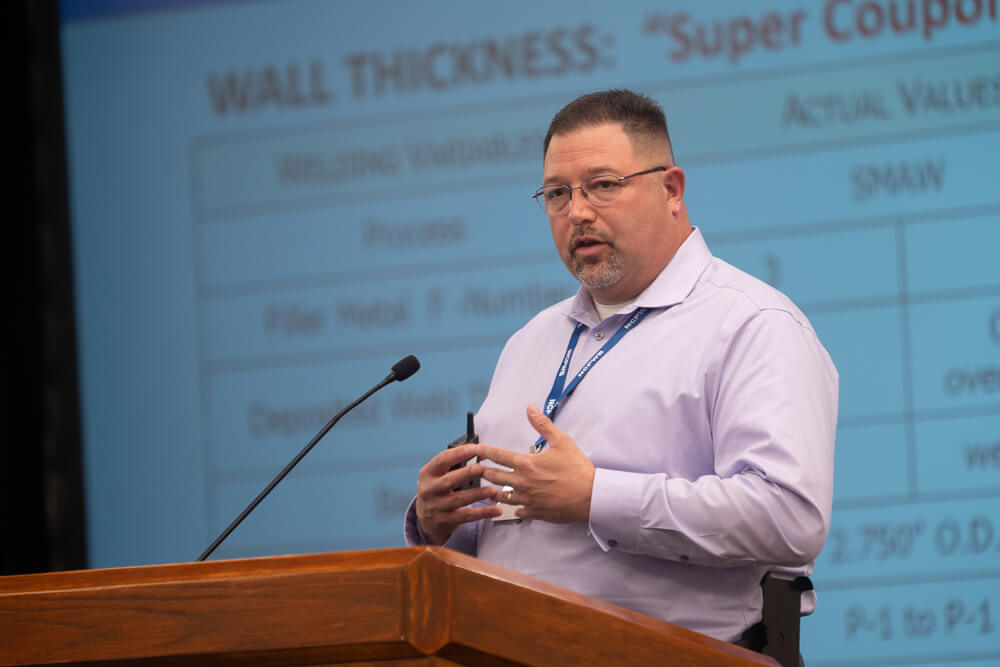
Robert Derby, Training Specialist with the UA, unveiled insights into the rationale behind redundancies in welder qualification tests, aimed at ensuring welders and welding operators are adequately prepared for specific job site requirements. The presentation delved into comparisons among the UA tests such as UA-2, UA-21, UA-60, and UA-81, revealing areas of overlap and divergence. Redundancies in qualification tests serve a crucial purpose: to validate proficiency across a spectrum of variables consistent with real-world welding scenarios.
The committee meeting portion of the event covered topics such as policy and procedures regarding the joint UA/NCPWB welder certification program and addressed chapter inquiries. In addition to the annual event, a one-day chapter operations seminar educated chapter administrators about the policies and procedures associated with maintaining welder qualification records.
Mark Your Calendar & Plan to Join Us Next Year
Mark your calendar for the NCPWB 2025 Annual Technical Conference/Committee Meeting, April 28 – April 29, 2025 in Clearwater Beach, FL. Watch mcaa.org and the National Update for additional information as the event gets closer.