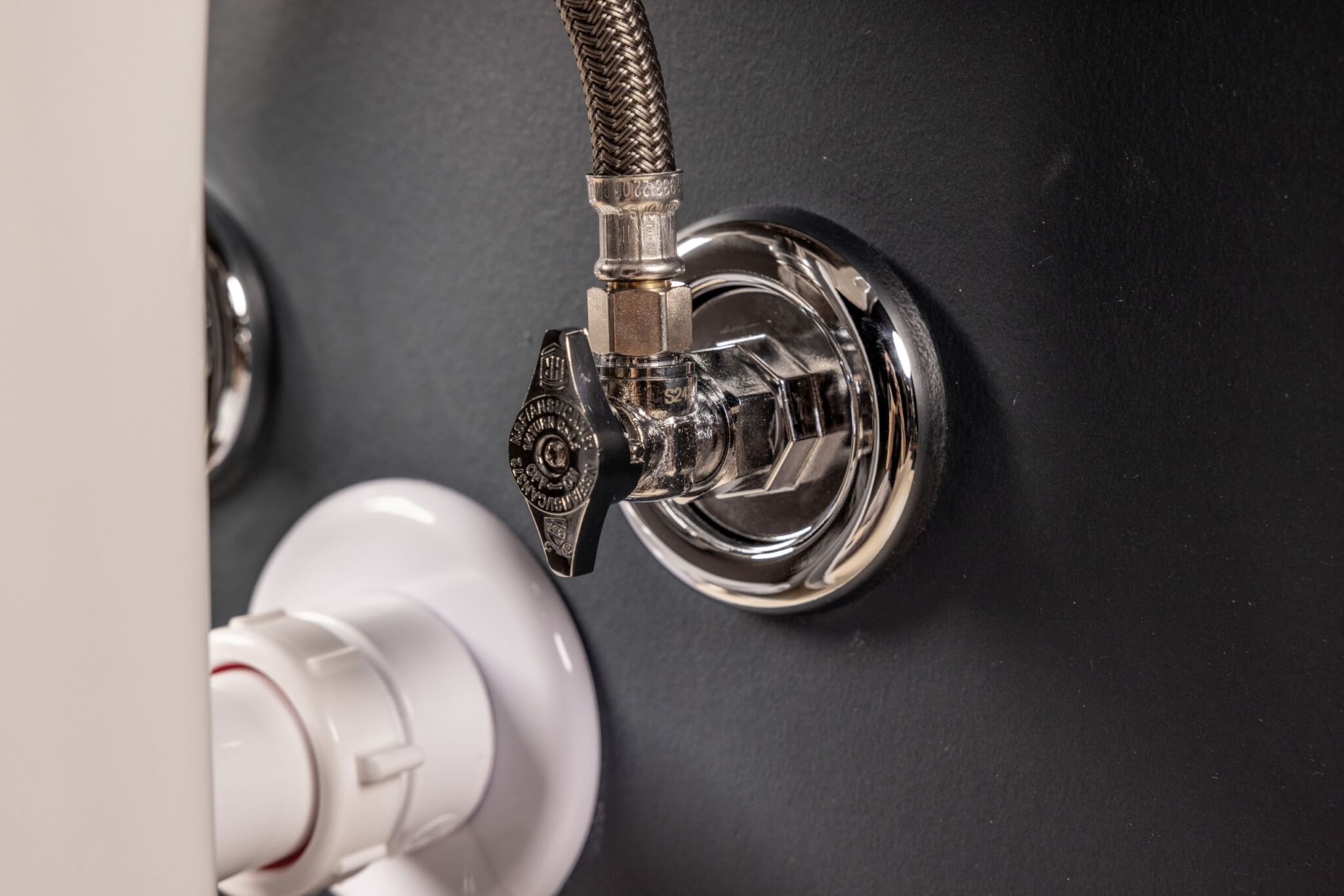
As the trades continue to navigate an ongoing labor shortage, innovative products and methods of installation become increasingly important. Over the past decade or so, one such product that industry professionals have gravitated toward is outlet boxes for new construction. The options run the gamut, from fixtures to washing machines to ice makers, and they offer a more efficient alternative to traditional rough-in plumbing methods for these kinds of installations. Here are the key reasons why outlet boxes are becoming the industry standard and how they can support your workflow, bottom line, and craftsmanship.
1. Outlet boxes save time.
Outlet boxes help you complete stub-outs more easily and earlier in the building process. The design of the product streamlines both pre-installation planning as well as the on-site work.
When planning out the needs for a project, you often have to consider which parts you need and how many of each you will have to order to complete the job. With old-school methods, whenever you had to install different water supply lines—such as those for washing machines and sinks—you had to collect several parts: brackets, clamps, caps, fixture stops, hammer arrestors, and sanitary plates.
Outlet boxes consolidate a lot of those different elements into one ready-to-go product, so there are fewer parts to order. That makes outlet boxes not only time-efficient but also cost-effective, as you can cut the number of parts ordered almost in half.
On the jobsite, outlet boxes continue to save you time. In traditional methods, the process involves several time-consuming steps. During the rough phase, bracketing is installed, then stub-outs are installed or secured. Next, the stub-out is connected to the water supply and tested. In the final phase, the stub-out is cut, cleaned, and deburred. Preparation for the supply stop is next, including applying flux, tape, etc., and installing escutcheons. The supply stop is then attached in the proper position, and a final test is performed.
However, with outlet boxes, the steps are simplified. During the rough phase, the outlet box is attached to a stud or bracket. Next, it is connected to the water supply, and a test is conducted. In the finish phase, the debris cover is removed and replaced with an escutcheon or trim plate.
2. Outlet boxes are versatile.
Not only can you find outlet boxes that consolidate multiple parts into a single solution, but you can also find options that work with multiple connection points. While some manufacturers use dedicated connections, others, like HoldRite from Reliance Worldwide Corporation, offer different tail pieces that are compatible with different pipe types and connection methods using the same outlet box. Those tail pieces can also have near 360-degree movement for installation in any orientation.
Additionally, you can find outlet boxes with fire-rated options if you need to install one on a shared wall. You can also get versions with and without hammer arrestors, depending on code requirements in your area.
3. Outlet boxes produce a professionally finished result.
Aside from functionality, outlet boxes also take aesthetics into account. For instance, HoldRite fixture boxes come with chrome and white trim plate options that you can match to the overall appearance of the area. These finishes thread into place, so there is no need for adhesives or fasteners. You can also find outlet boxes with other high-end finishes, such as washing machine boxes with contoured, white, paintable trim covers, along with chrome valves and water hammer arrestors.
These options allow you to not only work faster, but also customize the installation so it matches the aesthetic of the overall design. Outlet boxes provide time- and cost-savings along with professional results that you can be proud of.
For more information, visit www.holdrite.com.